Time of Flight (ToF) Image Sensors
Time-of-Flight sensors or ToF sensors are an active sensing technology for real-time depth sensing applications. Like LiDAR sensors, structured light cameras and stereo cameras, ToF sensors can “see” depth and are useful for a wide range of machine vision applications where accurate depth information is required.
ToF sensing technology has some limitations, but it offers advantages over other depth sensing technologies under the right operating conditions. ToF cameras have no moving parts, can be extremely compact, and are relatively inexpensive to produce. ToF cameras are particularly useful for real-time applications, since they can provide highly accurate depth information at up to 60 frames per second.
How does Time-of-Flight work?
Direct and Indirect Time-of-Flight (iToF and dToF)
There are two distinct approaches used in Time-of-Flight systems, each with their specific advantages within a given application. Direct ToF (dToF) cameras use a short light pulse, only a few nanoseconds in duration, and then directly measure the delay between the time the light pulse was emitted and the time an object in the scene reflects the light back to the camera. The distance from the camera to the target can be calculated based on the speed of light.
Indirect Time-of-Flight, or iToF cameras are a variation of ToF cameras. While ToF cameras directly measure the time it takes for the emitted light to be reflected back to the camera, indirect ToF cameras send out continuously modulated pulses of light, and then measure the phase shift of the frequency of reflected light pulses to calculate the distance to an object. Indirect Time-of-Flight technology can be useful for measuring objects that are close to the camera, and it can allow iToF cameras to operate with higher frame rates.
Create Accurate Depth Maps with ToF sensors
Unlike standard image sensors, that record the scene in 2 dimensions, ToF sensors also record depth information – creating a fully 3-dimensional image. The raw data from the sensor can be visualized as a false color video, which shows the depth information in the scene using color, or it can be converted into a depth map, that can be rotated and examined from different angles.
CONVENTIONAL
NEW
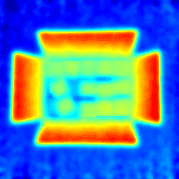
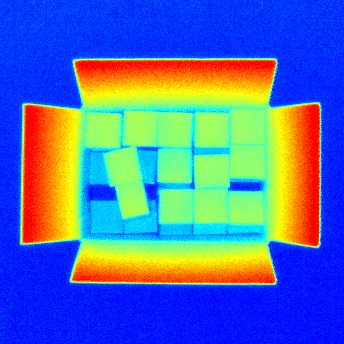
FSM-IMX570 Devkit for Vision System Engineers
FRAMOS has released a development kit to help engineers who are working to develop Time-of-Flight devices for industrial and robotics applications.
The FSM-IMX570 Devkit provides vision system engineers with a simple, coherent framework for quickly developing a working prototype of an indirect Time-of-Flight (iToF) camera system based on Sony’s industry-leading iToF technology.
CUSTOMIZING THE FSM-IMX570 DEVKIT FOR YOUR PROJECT
Devkit Customization Possibilities
- Customization of the Form, size, and layout of printed circuit boards (PCBs)
- Changes to optics and illumination to accommodate a desired working range or field of view
- Adjustments to illumination board light output (adjustments to working distance, or to match output to a particular laser product class)
- Tuning of Depth Processing to match a required working distance
- Driver compatibility support and driver functions for desired features
- Platform porting for compatibility and performance on a desired platform (TI, NXP, etc.)
- Periphery and interfacing (serialization, support for specific connectors)
What are ToF Cameras used for?
Industrial and Robotics Applications
ToF sensors and cameras are used for depth sensing in industrial and robotics applications, including providing machine vision for pick-and-place robots; object recognition on assembly lines; object classification for robotics; providing navigation capabilities for mobile robots; and for intrusion detection in industrial environments.
ToF Sensors in Logistics
ToF cameras are especially useful in a variety of logistics applications, including providing guidance systems for automated forklifts and Autonomous Guided Vehicles (AGVs), and for providing robots and automated equipment with collision prevention capabilities. ToF cameras are also used on packaging lines for package dimensioning and palletizing, and for inventory management.
ToF Sensors in Mobility and Transport
ToF sensors are being incorporated in the automotive industry and in agricultural vehicles for a variety of purposes, including operator identification and access control; behavior analytics; attention tracking (for self-driving vehicles); gesture recognition, and passenger surveillance.
Retail Automation
ToF cameras are also being adopted in the growing industry of retail automation, where they are used for a variety of purposes, including behavior analytics; object counting, and people tracking and localization, and flow analysis (to observe how they move through the space). ToF cameras and ToF sensors are also used to provide functionality for seamless checkout systems.
Sony ToF Sensors
SONY IMX556PLR-C
SONY IMX570PLR-C
Pioneering ToF Sensors for Easy-to-Use 3D Camera Applications
Sony’s IMX570 ToF sensor is a Back-Side Illuminated, indirect Time-of-Flight 3D image sensor for machine vision applications. The new IMX570 is a 1/4.5” type VGA sensor with 5 µm pixels.
Applying Sony’s sensing and ranging technologies, this compact, high-resolution sensor acquires precise depth data over operating ranges from 1.25m to 7.5m.
Key Features of Sony’s New IMX570 Sensor:
- Delivers high-resolution 3D images
- Suppresses blur of moving subjects
- Reduces processing load
- Improves robustness in all environments
FREQUENTLY ASKED QUESTIONS ABOUT ToF
LET US ANSWER ANY QUESTIONS YOU HAVE ABOUT IMAGE SENSOR TECHNOLOGIES OR REQUEST A SAMPLE TODAY.